La arquitectura y la tecnología están fuertemente vinculadas, siendo esta relación totalmente evidente en los edificios y construcciones de la revolución industrial. La famosa frase “La forma sigue a la función”, acuñada por la alemana Bauhaus (originalmente, la Staatliche Bauhaus, Casa de la Construcción Estatal) desde sus comienzos se refleja en el edificio diseñado por Walter Gropius, que fue su sede en Dessau, Alemania, entre 1925 y 1926. Sus volúmenes son independientes entre sí, y cada uno fue diseñado para la función para la que fue concebido. Además de esta relación entre la forma y la función, el manifiesto de la Bauhaus reivindicaba la unidad de los artistas, incluyendo entre estos a los arquitectos, y la vuelta al trabajo artesanal, “(…) construir un nuevo gremio de artesanos sin las barreras de clase que pretenden crear un muro entre los artesanos y los artistas (…)” e incorporar los productos diseñados a la producción industrial, convirtiéndolos en asequibles para el gran público.
Aunque ya han pasado 80 años desde que la Bauhaus cerró sus puertas, estos principios pueden recuperarse en el siglo XIX gracias a la impresión 3D, una nueva tecnología que, entre sus muchas aplicaciones, puede llegar a revolucionar la arquitectura de distintas formas, desde los diseños a los materiales usados, pasando obviamente por el proceso de fabricación.
El primer ejemplo del que tuvimos noticia en enero de 2013 fue la Landscape House, un edificio con forma de cinta de Möbius, ideado por Universal Universal Architecture en Amsterdam, diseñado por el arquitecto Janjaap Ruijssenaars, y que será impreso de una sola vez con una enorme impresora en 3D creada por el robotista italiano Enrico Dini. La estructura impresa en 3D consiste en una sola pieza, con acero y cristal en los lados. Según el diseñador, la casa está llamada a “celebrar el paisaje”, integrándose en el mismo, pero también se considera un experimento para comprobar la eficiencia de esta tecnología en la construcción de edificios.
La impresora (llamada D-Shape) crea una sustancia similar a la arenisca mezclando arena, u otros materiales similares, con un agente aglomerante, formando así capas cuyo espesor puede ser tan pequeño como 5 mm; la tremenda estructura de esta impresora permite manejar objetos de 6 metros en cada dimensión. Cada impresora puede manipular 2500 m2 de material al año, que equivaldría a 12 casas pequeñas, y puede trabajar en caso de necesidad en tándem con otras impresoras. Otros aspectos relacionados con la eficiencia es la velocidad, pues se supone que esta impresora construirá casas 4 veces más rápido que los métodos de construcción normales. En cuanto al precio, el pabellón construido por Dini en Pontedera, una instalación que parece más bien una escultura, no ha costado más que 200 euros. Y finalmente, claro, hay que tener en cuenta el ahorro de personal, ya que la construcción será completamente automática. El proyecto vio la luz en 2014.
Por otro lado, un proyecto holandés pretende construir una de las tradicionales casas que pueden verse junto los canales de Amsterdam. Este proyecto es de la firma DUS Architects, y consiste en un pabellón que a su vez imprime otros pabellones. Esencialmente, es una versión gigante de la impresora de escritorio Ultimaker, a la que han llamado Kamermaker, que han rodeado de un contenedor plateado de 3.5 m de altura. En este caso, el material en que se construya la casa será un entramado de componentes de polipropileno unidos entre sí por un cable de acero, en el caso de la fachada.
Para las habitaciones, tal como deciamos al comienzo, se han basado en la premisa de la Bauhaus, ya que cada una será una oportunidad de explorar nuevos métodos de imprimir, usando un nuevo material y dando la oportunidad de estudiar cada ángulo, en función del papel de cada compartimento. De este modo, la habitación destinada al almacenaje ha sido pensada como habitación de reciclaje trabajando en conjunto con una empresa de desechos, mientras que para la cocina se han planteado usar como material el almidón de patata.
Entrando en un concepto más radical, está el proyecto de Softkill Design, que realmente sería imposible de construir con mortero y ladrillos. Aunque el aspecto es más similar a un escenario, o incluso procedente una película de terror que a una casa, el objetivo del proyecto es centrarse en la optimización estructural, en construir solo lo necesario para funcionar; esta optimización hace que la estructura sea más fibrosa y la impresión 3D el método perfecto para construirla. La Protohouse 1.0 vio la luz tras año y medio de trabajo, y es un modelo de casa modelado e impreso a escala a partir de 30 piezas interconectadas. El algoritmo usado por Softkill imita la estructura del hueso, en búsqueda del balance óptimo entre la forma y la fortaleza estructural, usando la técnica de Sinterización por Laser Selectiva (SLS). A pesar de su apariencia, la Protohouse 1.0 es muy útil para ilustrar los problemas a los que se enfrentarán los arquitectos cuando impriman casas. Toda ella está impresa de una vez, interior, exterior, huecos para fontanería y cableado eléctrico, alfombras, sillas, incluso las bisagras y los pestillos de ventanas y puertas, usando un tipo de resina plástica que debe realizar multitud de funciones. Encontrar el material adecuado para cubrir todas estas necesidades es un reto en sí.
Siguiendo el ejemplo de la “democratización” del que hablaban DUS Architects, el proyecto actual es la Protohouse 2.0, la casa que quieren que la gente descargue e imprima por sí misma. No será muy grande (4 m x 8 m y casi 3 metros de altura) pero estará más cerca de ser una casa terminada de lo que podríamos reconocer. Incluso si alguien no quiere la casa completa, puede (como en el caso de la casa del canal) descargar objetos individuales y usarlos para mejorar su propia vivienda.
La repercusión ambiental
Partiendo de los ejemplos anteriores, y centrándonos en el aspecto ambiental del uso de la impresión 3D en la arquitectura, podemos citar dos aspectos principales.
En primer lugar, la cuestión de las escalas. A este respecto, incluso la prestigiosa revista The Economist afirmaba que el principal avance de esta tecnología consistía en el abaratamiento de los costes de producción (para lo cual antes se consideraba que era necesaria la producción en masa), y también una reducción de gran parte de los residuos generados. Un solo artículo podría crearse por el mismo coste unitario de crear miles de ellos.
El problema de las escalas está ligado también a la centralización de la manufactura: actualmente, el proceso de fabricación se localiza en los polígonos industriales de los medios urbanos, y de allí los productos se llevan a todos los rincones del planeta (lo que conlleva unos gastos de transporte, así como la contaminación derivada del mismo). La descentralización de la manufactura, ligada a la impresión 3D, haría desaparecer a su vez la necesidad de concentrar estos empleos en zonas industriales, los gastos de transporte, e incluso la necesidad de deslocalizar estas mismas fábricas en países donde los costes de producción son menores. A esta conclusión llegó también Joshua Pearce, un profesor asociado de ciencia de los materiales e ingeniería electrónica e informática de la Michigan Technological University tras llevar a cabo un análisis económico de ciclo de vida de la impresión 3D en una economía americana media. Su estudio demostró que fabricando material en una impresora 3D produce un menor gasto energético (y por tanto libera menor cantidad de CO2) que produciendo esa misma pieza en una fábrica y transportándola al centro comercial. El análisis fue llevado a cabo con distintos productos y el resultado al que llegaron fue que los artículos impresos en la máquina doméstica precisaron del 41 al 64 % menos de energía que fabricándolos en algún país de Asia, y transportándolos a los USA (y aún más si se utilizan impresoras 3D solares). Por otro lado, la impresora doméstica también permite el ahorro de materia prima, al permitir la creación de productos huecos manteniendo la estabilidad de la estructura. El estudio completo puede leerse en el artículo Environmental Life Cycle Analysis of Distributed 3D Printing and Conventional Manufacturing of Polymer Products publicado por la revista especializada ACS Sustainable Chemistry and Engineering.
Otro aspecto que incide en la escala de la construcción, es el uso de impresoras de gran tamaño con estructuras similares a las grúas de caballete. Un profesor de la Universidad del Sur de California, Behrokh Khoshnevis, creó para ello un nuevo mecanismo de extrusión que permite extruir cemento húmedo, combinado con una paleta y un endurecedor especial, dando la forma según se imprimen las distintas capas, manteniendo una determinada viscosidad del cemento. A esta técnica se la denomina construcción en contornos. Con este método, el profesor ha construido muros de 6 pies (dos metros) de alto, con capas de 6 pulgadas (15 cm) de altura y 4 pulgadas (10 cm) de espesor, y cree firmemente que pueda ser aplicado a edificios completos, afirmando que con esta construcción de contornos es posible fabricar la estructura completa de una casa de 185 m2 en menos de 20 horas. La impresora 3D, montada sobre una grúa de puente, y con un peso de aproximadamente 500 libras (226 kg), podría ser llevada a donde se realizara la construcción, donde fabricaría los contornos como lo haría una RepRap gigante, usando el suelo como plataforma o, posiblemente con una impresora usando como base la propia casa (a este respecto, hay que decir que Nicholas Seward, inventor de la RepRap Simpson, ya ha creado una impresora 3D montada sobre un muro, llamada Wally), capa tras capa y volviendo al suelo tras completar el trabajo. También sugirió colocar los brazos de la impresora en raíles, de forma que pudieran imprimir una casa y deslizarse para construir otra, haciendo posible imprimir barrios enteros rápidamente.
Esta posibilidad de construir edificios eficientes y baratos, frente las técnicas actuales, que según el profesor Khoshnevis son “derrochadoras y emisoras de gran cantidad de emisiones, además de promover la corrupción, con costes siempre por encima del presupuesto”; además de reducir los accidentes de construcción, que provocan sólo en EEUU 400,000 personas heridas, y de 6,000 a 10,000 personas muertas cada año.
Este abaratamiento de la manufactura, llevaría a su vez a que cualquier aldea rural con escasos recursos, que tradicionalmente son excluidas de las nuevas tecnologías y materiales de construcción, podría disponer de una de estas impresoras. En este punto, se va haciendo conocido el proyecto de OpenSourceEcology, una plataforma opensource (de código libre), que incluye entre sus proyectos el GVCS (Global Village Construction Set), una colección de 50 máquinas de código abierto, fácilmente realizables con materiales baratos, y que incluye, entre tractores, placas solares, molinos eólicos y otros artilugios, una impresora 3D. Y según narra recientemente su blog, una casa, que han llamado Microhouse, y cuyo desarrollo podéis ver en el Log de Chris Reinhardt. Aunque no han utilizado la impresión 3D en su fabricación, utilizán una máquina de extrusión para realizar ladrillos de adobe in situ, con los que se construye la casa.
Materiales
Otra cuestión con implicaciones ambientales sería la referente a los materiales usados en la impresión 3D. Los más utilizados en las impresoras domésticas son plásticos de distintos tipos, siendo de los más utilizados y más populares en la industria el plástico ABS (Acrilonitrilo Butadieno Estireno), debido a su gran dureza y su rápido enfriamiento, ya que se usa para fabricar parachoques para coches, o los famosos juguetes LEGO. Su desventaja, sin embargo, radica en su procedencia, el petróleo, y en que es un material no biodegradable.
Algunas alternativas en cuanto a materiales plásticos, junto con el reciclaje del propio ABS, es el PLA (Ácido Poliláctico) un bioplástico procedente del maíz que, además, es biodegradable, y que ha sido utilizado por la firma de arquitectos Smith y Allen para crear un recinto en un bosque californiano, llamado Echoviren y cuya “sostenibilidad” se basa en su capacidad de descomponerse de forma natural en un plazo de 30 a 50 años. El PLA también se ha utilizado en el proyecto de la casa del canal que se comenta más arriba de este articulo.
Otro ejemplo de material plástico es el PHB (Polihidroxibutirato), o biopropileno, aunque en el caso Incluso se está experimentando con bacterias capaces de fabricar plásticos, a través del metabolismo de azúcares. Además de estos materiales plásticos, se está investigando en otros de mayor dureza y durabilidad, como por ejemplo la cerámica o el cemento (como era el caso de la Landscape House). Un estudio de Oackland denominado Emerging Objects, realmente el proyecto de dos arquitectos, Ronald Rael y Virginia San Fratello, ambos profesores en un estudio de 3D en Berkeley, han decidido centrarse en investigar este aspecto de la impresión 3D (y no son los únicos). La novedad de estos arquitectos es que esos materiales que investigan son orgánicos y renovables: sal recogida en la bahía de San Francisco, pulpa de madera, arcilla… Usando una impresora 3D estándar basada en polvo, ellos y sus alumnos inventan cómo imprimir ladrillos, componentes y muebles usando materiales reciclables. La madera impresa es bastante realista, debido al grueso grano que se obtiene en el proceso de manufactura en capas. La sal, por el contrario, parece “leche sólida”, usando las palabras de Rael. Todos estos materiales, al contrario de lo que se podría pensar, son muy fuertes pues se usan técnicas de refuerzo creadas por ellos mismos. Su cemento impreso es también más fuerte que el estándar. Y lo que es más importante, es un 90% más barato que la tecnología de impresión 3D actual.
Esto abre la mente a la posibilidad de conseguir los materiales necesarios a partir de fuentes locales, donde además del ahorro les seduce pensar en las costumbres y usos localesresurgiendo en la arquitectura, o ver ciudades resolviendo problemas de infraestructura usando materiales locales. O incluso la posibilidad de sustituir ladrillos de las paredes usando otros diseñados por uno mismo. Además de estos materiales, en una entrevista realizada al respecto en la página Makezine, Rael hablaba del posible uso del papel reciclado, con el cual han fabricado distintas piezas.
Dentro de la investigación en ciencia de los materiales, si la Protohouse se basaba en el algoritmo que siguen las fibras de hueso usando bioresinas, un equipo del MIT, Mediated Matter, trabaja sobre medios de fabricación inspiradas en la biología que va más lejos aún: usar gusanos de seda como “albañiles”, aprovechando y maximizando la fortaleza estructural y tensional del hilo de seda extendido sobre una estructura previamente creada con un brazo robótico que permite crear formas que no pueden ser conseguidas con la impresión 3D convencional. El Silk Pavilion (Pabellón de Seda) es la construcción más grande construida de este modo. Mediated Matter descubrió que los gusanos emigran de forma natural a las áreas más oscuras, creando paneles más fuertes cuanto más alejados estuvieran del Sol. Los efectos de luz informan sobre las variaciones en la organización (densidad) del material. Los gusanos dejaron un agujero en la estructura, en línea con el sol, que actúa a modo de reloj solar. Al escanear sus movimientos y analizarlos, obtuvieron un algoritmo que les permitirá crear estructuras tan fuertes como las creadas por ellos. No obstante, el Pabellón de seda carece de uso práctico, al ser más un experimento artístico por el momento.
Para terminar con el repaso a los materiales, existe un proyecto que pretende crear cristal usando arena y energía solar, por medio de una impresora 3D, considerado por los expertos como un prometedor primer paso en esta dirección. La máquina fue diseñada por el alemán Markus Kayser y se denomina Solar Sinter, tomando por tanto el nombre de su fuente de energía y de la técnica que utiliza, la sinterización, que convierte una sustancia pulverulenta en un sólido por medio del calor. Kayser desarrolló esta máquina en 2010, durante sus estudios en el Reino Unido. Según él, este proceso podría convertirse en el modo más efectivo (en relación a los costes). La lente cuesta unos 600 dólares, lo cual la hace más barata que la mayor parte de dispositivos parabóliocos usados para capturar luz en el desierto, y el proceso podría llegar a producir gran variedad de artefactos, desde recipientes de cristal, a las superficies de los paneles fotovoltaicos. Por el momento, una compañía de cerámicas se ha interesado en las aplicaciones de la Solar Sinter y patrocinado los últimos viajes de investigación de Kauser al desierto marroquí. En este caso, como en el de Emerging Objects, la idea principal es la producción in situ utilizando los materiales y fuentes de energías disponibles en cada lugar. Para este efecto, el anteriormente mencionado profesor Koshnevis estuvo también investigando la posibilidad de construir usando material lunar, y en general para el caso de zonas áridas, donde el agua es un recurso limitante como en la luna a la hora de seleccionar los materiales.
Sin embargo, además de los materiales, según afirma el profesor Koshnevis, es importante la selección de nuevas geometrías adaptadas al medio donde se va a construir. La construcción en contornos que propone puede construir estructuras similares a las fabricadas con adobe, hecho con barro, arcilla y paja, y otros materiales domésticos, en África, Asia y muchas partes de América, que dura miles de años. Pero en realidad, es el uso de geometrías curvas, lo que da como resultado una mayor estabilidad que los cubos tradicionales. Este factor es especialmente importante, en zonas con alto riesgo sísmico.
Otras aplicaciones sostenibles
Finalmente, y en relación a las aplicaciones de la impresión 3D, hay algunas muy interesantes a tener en cuenta. Además de las piezas que imprimimos y diseñamos por primera vez, como los jarrones, ladrillos o bandejas de diversos materiales, se puede alargar la vida útil de los objetos que ya tenemos en casa, de dos distintas maneras.
En primer lugar, cabe la posibilidad de perder una pieza, o que se rompa, siendo imposible, o muy difícil adquirir otra, o incluso que sea sorprendentemente más cara que el aparato en su totalidad. En este ejemplo de Instructables realizado por Ben Chapman, aunque no se trate de arquitectura, se puede ver cómo arreglar una lámpara para la bici, en la cual se había roto la unión con el manillar, fabricando una nueva unión mediante impresión 3D. Otra forma de alargamiento de la vida útil, es el que se refiere a imprimir objetos que añaden una nueva función y por tanto, alargan la vida útil de otros artículos, como en este proyecto RE de Samuel Bernier, también de Instructables en el que una jarra de cristal, que iba a ser desechada, y cuya fabricación requiere de grandes cantidades de energía, se convierte en un exprimidor de naranja, eliminando también la necesidad de fabricar este último.
Cuando hablamos de edificios, este reciclaje de estructuras antiguas y aprovechamiento de los residuos para crear nuevas, es posible gracias a un robot reciclador de Cemento llamado ERO, una máquina que dispara agua a alta presión sobre el cemento, provocando la ruptura, y recogiéndolo para su reutilización, éste podría ser un buen complemento a las impresoras 3D para uso en construcción.
Ytong, la alternativa sencilla y eficiente
En la actualidad la arquitectura vive un momento de profunda transformación en cuanto a los requisitos de habitabilidad, bienestar interior y eficiencia energética y de todo el proceso constructivo. Entre los muchos sistemas que han ido surgiendo para impulsar estos cambios encontramos los bloques de hormigón celular de Ytong.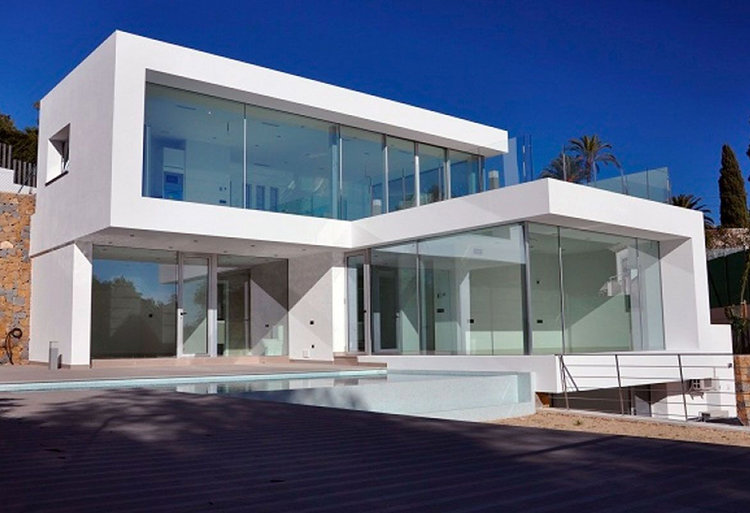
Pero no se trata tan solo de unos bloques, Ytong cuenta con toda una serie de elementos y un sistema constructivo propio que nos permitirá construir viviendas de elevada eficiencia energética y un elevado confort interior sin tener que recurrir al gran número de materiales y técnicas diferentes necesarias en una vivienda construida con un sistema más tradicional. Aunque es un producto casi centenario (el hormigón celular Ytong se creó por primera vez en 1924), poco a poco ha ido adquiriendo relevancia en el sector de la construcción. El hormigón celular Ytong se compone de una mezcla de arena, cal, agua y una pequeña cantidad de polvo metálico, curado en autoclave y cortado en bloques de gran precisión.
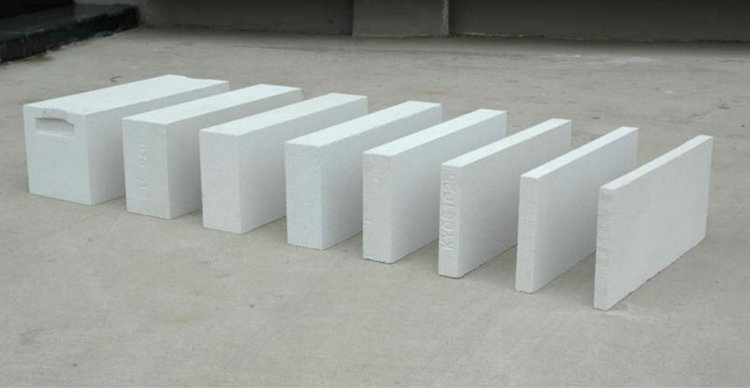
El sistema se compone principalmente de unos bloques de 62,5 x 25 cm con diferentes espesores que van de 5 a 36,5 cm. El otro componente esencial del sistema es un mortero cola que se aplica en muy pequeñas cantidades y que mantiene unidos los bloques. Por último, dispone de piezas especiales para forjados, cubiertas, dinteles y zunchos. La ventaja es que nos permite construir con muy poca variedad de elementos y materiales, lo que simplifica y agiliza tanto los pedidos como la obra en sí.
El proceso constructivo es relativamente sencillo, de hecho lo podría hacer cualquiera con un poco de maña y con la ayuda de un arquitecto. Los bloques son muy ligeros y fácilmente manejables ya que disponen de asas, van machiembrados para facilitar su colocación y se pueden cortar fácilmente, incluso con una sierra de mano, para ajustarlos a las medidas necesarias. Las irregularidades que puedan ir surgiendo según se van apilando bloques y formando los muros se lijan manualmente. El resultado son unos muros, tabiques y forjados muy lisos en los que solo queda incorporar los acabados.
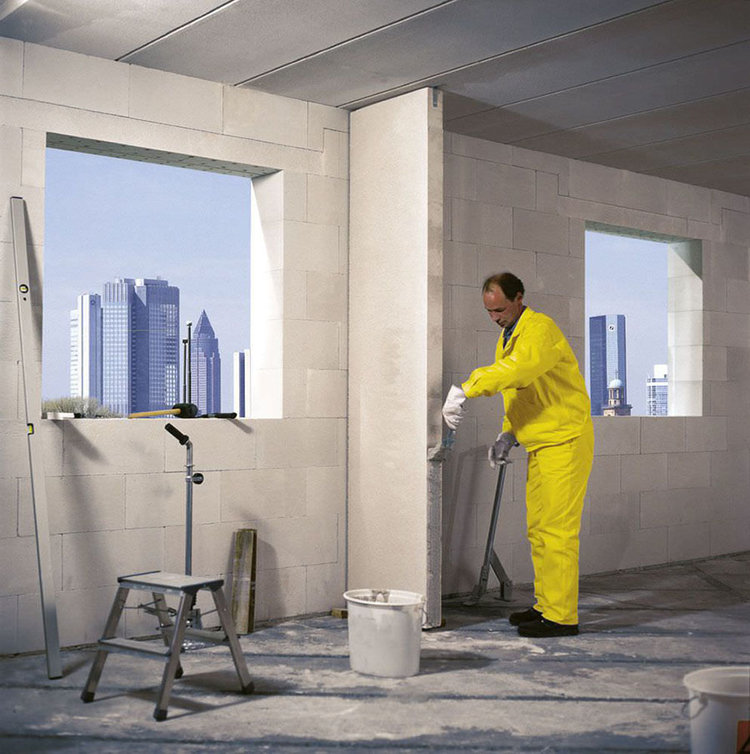
Para empezar a construir necesitaremos una base de mortero fresco impermeabilizada y bien nivelada donde apoyar la primera hilera de bloques. Como ya hemos dicho antes, los bloques son muy ligeros, solo el 20% de ellos es sólido, el resto son diminutos poros cerrados que le confieren unas magníficas propiedades térmicas, aislantes y acústicas.
Otro aspecto interesante del sistema es que al ser de por sí un buen aislante térmico, no requiere de más capas (en España al menos, nos podríamos ahorrar el aislante térmico), la fachada del edifico estará compuesta de una sola hoja formada por estos bloques, los acabados se aplican directamente sobre los muros Ytong.
En cuanto a su fabricación, se realiza en autoclave y necesita una cantidad de energía menor que cualquier otro material tradicional comparable. Requiere 1m³ de materia prima para generar 5m³ de producto final. El polvo y los restos que se liberan a lo largo del proceso y al realizar los cortes no son contaminantes y de hecho son reutilizables y se incorporan de nuevo a la cadena de producción como materia prima. Se trata por tanto de un material respetuoso con el medio ambiente y totalmente reciclable.
Las instalaciones van empotradas en rozas que se realizan en los muros con ayuda de la sierra de ranurar para las más pequeñas y la sierra eléctrica las más voluminosas. También dispone de piezas estructurales para forjados y cubiertas que llevan incorporada una armadura, pudiendo alcanzar vanos de hasta 6,60 m y voladizos de 1,5 m.
Para rematar, los bloques de hormigón celular Ytong son incombustibles y muy poco sensibles a los choques térmicos de manera que en presencia de fuego no se fisuran, no estallan ni liberan ningún tipo de gas nocivo. De hecho son una muy buena opción para construir cortafuegos.
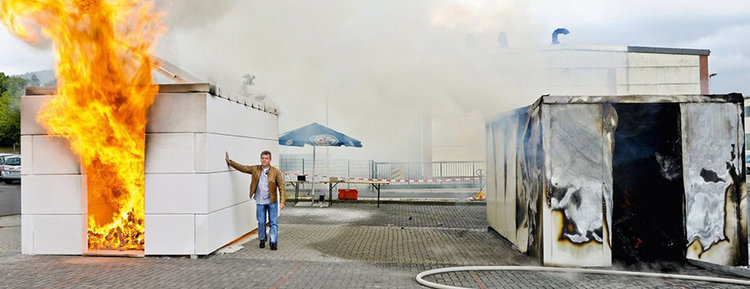
En resumen, el sistema Ytong constituye una alternativa eficaz y completa frente a los sistemas tradicionales consiguiendo además mejores resultados en cuanto a aislamiento y eficiencia energética e incluso reduciendo costes y tiempo de construcción. Incluso la complejidad de sus soluciones constructivas es menor que en otros sistemas. Sin duda se trata de una opción a tener en cuenta si buscamos una vivienda más respetuosa con el medio ambiente y eficiente en todos los sentidos.
No hay comentarios:
Publicar un comentario